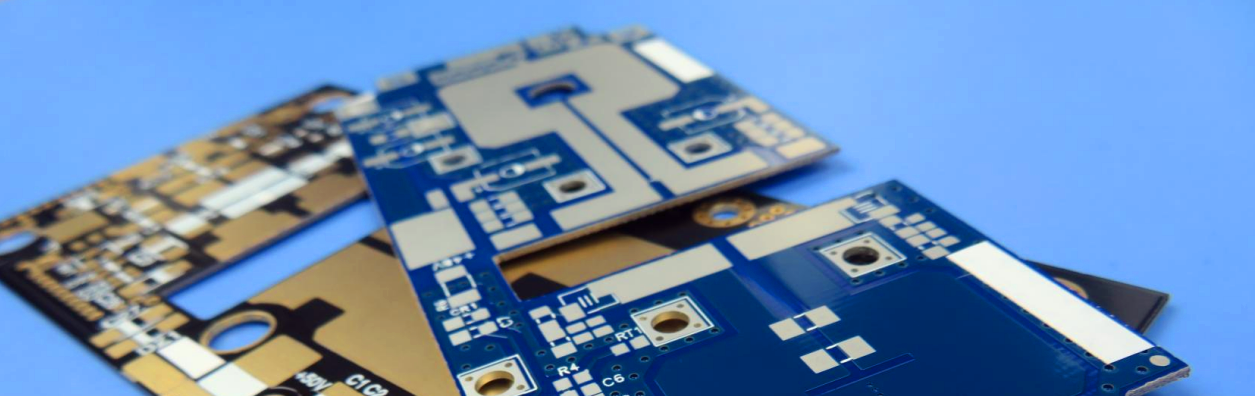
Call Us Now !
Tel : +86 755 27374946
Order Online Now !
Email : info@bichengpcb.com
The Future of High-Frequency PCBs–Trends, Challenges, and Innovations The global PCB industry is undergoing a transformative phase, driven by the rapid adoption of advanced technologies such as 5G, IoT, and satellite communications. Over the past six months, several key trends have emerged, shaping the future of high-frequency PCBs and creating new opportunities for manufacturers and suppliers. As a leading player in the high-frequency PCB market, we are at the forefront of these developments, delivering cutting-edge solutions to meet the evolving demands of industries such as aerospace, telecommunications, and defense. Industry Trends Shaping the High-Frequency PCB Market 1. 5G Expansion and Beyond The rollout of 5G networks continues to accelerate worldwide, with countries investing heavily in infrastructure to support faster data speeds and lower latency. This has created a surge in demand for high-frequency PCBs capable of handling higher frequencies with minimal signal loss. According to recent reports, the 5G PCB market is expected to grow at a CAGR of over 15% through 2028, driven by the need for advanced materials and innovative designs. 2. Satellite Constellations and Space Exploration The rise of satellite constellations for global connectivity and space exploration has significantly increased the demand for high-reliability PCBs. These applications require materials that can withstand extreme temperatures, radiation, and mechanical stress while maintaining stable electrical performance. The growing interest in low Earth orbit (LEO) satellites and deep-space missions has further emphasized the need for robust PCB solutions. 3. Military and Defense Modernization Governments worldwide are investing in the modernization of military and defense systems, including radar, communication, and surveillance technologies. High-frequency laminates PCBs play a critical role in these systems, enabling precise signal transmission and reception. The demand for lightweight, durable, and thermally stable PCBs in this sector is expected to remain strong in the coming years. 4. Sustainability and Material Innovation As the industry moves toward more sustainable practices, there is a growing focus on developing eco-friendly materials and manufacturing processes. Manufacturers are exploring ways to reduce waste, improve energy efficiency, and use recyclable materials without compromising performance. This trend is particularly relevant in the high-frequency PCB segment, where material properties are critical to performance. Innovations in High-Frequency PCB Materials In response to these industry trends, we are proud to introduce the F4BTMS series, a next-generation material designed to meet the demanding requirements of modern high-frequency applications. Building on the success of our F4BTM series material, the F4BTMS1000 incorporates advanced ceramic and glass fiber technologies to deliver superior performance in aerospace, telecommunications, a...
The Rise of HDI Hybrid PCBs and the Latest Innovations in High-Frequency Materials As we step into 2025, the PCB industry continues to evolve at a rapid pace, driven by the increasing demand for high-performance, high-density interconnect (HDI) PCBs and advanced materials that cater to the needs of cutting-edge technologies such as 5G, IoT, automotive electronics, and aerospace applications. Among the most significant trends this year is the growing adoption of hybrid PCBs that combine high-frequency materials like Rogers RO4003C with traditional FR-4 laminates. These hybrid PCBs offer a unique balance of performance, cost-effectiveness, and manufacturability, making them ideal for a wide range of applications. In line with this trend, we are proud to announce the successful shipment of our latestHDI Hybrid PCB: the 8-Layer 1.5mm RO4003C S1000-2M. This product exemplifies the industry's shift toward more sophisticated and high-performance PCB solutions, designed to meet the stringent requirements of modern electronic devices. The 2025 PCB Industry Landscape: Key Trends and Innovations 1. The Surge in Demand for HDI PCBs High-density interconnect (HDI) PCBs have become the backbone of modern electronics, enabling the miniaturization of devices while enhancing their performance. With the proliferation of 5G networks, IoT devices, and advanced automotive systems, the demand for HDI PCBs has skyrocketed. These PCBs feature finer trace widths, smaller vias, and higher layer counts, allowing for greater functionality in compact designs. 2. Hybrid PCBs: Bridging the Gap Between Performance and Cost Hybrid PCBs, which combine high-frequency materials like Rogers RO4003C with traditional FR-4 laminates, are gaining traction in 2025. These PCBs offer the best of both worlds: the superior electrical performance of high-frequency materials and the cost-effectiveness of FR-4. This makes them particularly attractive for applications such as RF/microwave circuits, automotive radar systems, and cellular base stations. 3. Advancements in High-Frequency Materials Materials likeRogers RO4003C are at the forefront of the PCB industry's evolution. With a dielectric constant (Dk) of 3.38 and a low dissipation factor (Df) of 0.0027 at 10GHz, RO4003C is ideal for high-frequency applications. Its thermal stability, low moisture absorption, and compatibility with standard FR-4 manufacturing processes make it a preferred choice for designers of RF and microwave circuits. 4. Sustainability and Environmental Compliance As environmental regulations become more stringent, PCB manufacturers are increasingly adopting eco-friendly materials and processes.Rogers 4003C, for instance, is non-brominated and free from harmful substances, aligning with global sustainability goals. Introducing Our Latest HDI Hybrid PCB: 8-Layer 1.5mm RO4003C S1000-2M Our newly shipped...
Advanced High-Frequency PCBs: Paving the Way for Future Applications The high-frequency PCB market in 2025 is a hotbed of activity, with trends and opportunities emerging at a breakneck pace. Recent market research indicates a staggering 30% year-on-year growth, driven by a confluence of factors. One of the most significant drivers is the automotive industry's shift towards electrification and autonomous driving. High-frequency PCBs are now integral to advanced driver-assistance systems (ADAS), with radar and sensor modules relying on their precision signal handling. A case in point is the new breed of electric vehicles that use high-frequency PCBs to manage battery management systems more efficiently, optimizing charging times and extending range. In parallel, the consumer electronics sector continues to fuel demand. Smartphones, tablets, and gaming consoles are constantly evolving, demanding higher frequencies and faster data transfer rates. Manufacturers are scrambling to meet this need, and our Bicheng company has positioned itself strategically. We are proud to announce our newly shipped PCB, the F4BTMS series. It is an upgraded version of the F4BTM series and has achieved remarkable technological breakthroughs. The material is enhanced with a significant amount of ceramics and reinforced with ultra-thin and ultra-fine glass fiber cloth. This results in outstanding material performance and a broader range of dielectric constants, making it highly reliable and suitable for aerospace applications, capable of replacing similar foreign products. By cleverly incorporating a small amount of ultra-thin and ultra-fine glass fiber cloth and a large amount of uniformly distributed special nano-ceramics mixed with polytetrafluoroethylene resin, we have minimized the negative effects of glass fiber on electromagnetic wave propagation. This leads to reduced dielectric loss, enhanced dimensional stability, and decreased X/Y/Z anisotropy of the material. It also broadens the usable frequency range, boosts electrical strength, and improves thermal conductivity. Moreover, the material shows excellent low thermal expansion coefficient and stable dielectric temperature characteristics. The F4BTMS series laminates comes with RTF low roughness copper foil as a standard feature, reducing conductor loss and providing excellent peel strength. It can be used with either copper or aluminum bases. For example, the F4BTMS615 PCB has a dielectric constant (Dk) of 6.15 at 10GHz, a dissipation factor of.0020 at 10GHz and 0.0023 at 20GHz. It features a CTE x-axis of 10 ppm/°C, CTE y-axis of 12 ppm/°C, CTE z-axis of 40 ppm/°C within the temperature range of -55°C to 288°C. It also has a low thermal coefficient of Dk at -96 ppm/°C from -55°C to 150°C, a high thermal conductivity of 0.67 W/mk, and a moisture absorption of 0.1%. Our new product is a 2-layer rigid PCB with a stackup of Copper_layer_1 - 35μm, F4BTMS615 Core - 5.08...
Servers Drive the PCB Industry Into the Growth Stage "Bicheng's New RO4360G2 PCB 24mil: Meeting the Demands of the Growing PCB Industry in the AI Era" In recent times, with the rapid development of AI applications, the demand for servers has surged, propelling the PCB industry into a new growth cycle. Prismark data indicates that the global PCB output value is expected to grow by 5.5% annually in 2024 and further increase by 6.2% in 2025. Notably, the annual compound growth rate (CAGR) of HDI and IC substrates stands at 7.8% and 7.6% respectively, highlighting the continuous expansion of product demand. Looking ahead to 2025, it is anticipated that Intel and AMD will introduce new-generation platforms - Birch Stream and Turin. These are expected to enter small-scale production in the first half of 2025 and mass production in the second half, leading to an upgrade in CCL grade to M7 and an increase in the number of board layers to over 20. This will bring comprehensive replacement and upgrading to the PCB industry, fulfilling the high-performance requirements of new-generation servers and enhancing the product value and market competitiveness of relevant supply chain manufacturers. Against this backdrop, the continuous expansion of the market share of AI servers provides long-term growth momentum for relevant supply chain manufacturers. Bicheng is proud to introduce its new product, the RO4360G2 PCB 24mil. Rogers RO4360G2 laminates are low loss, glass-reinforced, hydrocarbon ceramic-filled thermoset materials that strike an ideal balance between performance and processing capability. They are the first high dielectric constant (Dk) thermoset laminate that can be processed similarly to FR-4. These materials are lead-free process capable and offer enhanced rigidity for improved processability in multi-layer board constructions, while reducing material and fabrication costs. RO4360G2 laminates can be paired with RO440 series prepreg and lower-Dk RO4000 laminate in multi-layer designs. The features of RO4360G2 are remarkable. It has a dielectric constant of 6.15 +/- 0.15 at 10 GHz/23°C, a dissipation factor of 0.0038 at 10 GHz/23°C, a Td > 407°C, a high Tg greater than 280°C TMA, a high thermal conductivity of 0.75 W/mK, a low Z-axis coefficient of thermal expansion at 28 ppm/°C, and copper-matched coefficients of thermal expansion (-55 to 288°C) with X axis at 13 ppm/°C and Y axis at 14 ppm/°C. It is also lead free process compatible and has a 94V-0 flammability rating. The benefits of RO4360G2 high frequency PCB are numerous. It offers design flexibility, plated through-hole reliability, compatibility with automated assembly, and is environmentally friendly as it is lead free process compatible. Its efficient supply chain and short lead times make it a cost-effective material option. The PCB stackup of the RO4360G2 24mil Rogers PCB is a 2-layer rigid PCB with a copper layer 1 of 35μm, a Rogers RO4360g2 substrate of 24mil (0.61mm), and a copper la...
Advancements in High-Frequency PCBs Drive Innovation in the Electronics Industry Introduction: The rapid evolution of technology has led to increased demand for high-frequency printed circuit boards (PCBs) in various applications such as telecommunications, aerospace, defense, and wireless communication systems. High-frequency PCBs play a crucial role in enabling the transmission of high-speed and high-frequency signals with minimal losses. In recent years, significant advancements in high-frequency PCB manufacturing techniques, materials, and design practices have been driving innovation and pushing the boundaries of what is possible in the electronics industry. Material Innovations: One of the key factors influencing the performance of high-frequency PCBs is the choice of materials. Traditional PCB materials such as FR-4 have limitations when it comes to high-frequency applications due to their relatively high dielectric constant and loss tangent. To overcome these limitations, new materials with improved electrical properties have been developed. For instance, specialized materials like Rogers material, Teflon, and polyimide offer low dielectric loss, low moisture absorption, and excellent dimensional stability, making them ideal choices for high-frequency PCBs. Design Techniques: Designing a high-frequency PCB requires careful consideration of various factors such as trace widths, spacing, and impedance matching. Advances in design software and simulation tools have made it easier for engineers to optimize their high-frequency PCB designs. With the help of electromagnetic simulation software, designers can predict and mitigate signal integrity issues, reduce electromagnetic interference (EMI), and optimize the performance of their high-frequency circuits. Techniques like controlled impedance routing, differential signaling, and microstrip/stripline configurations are commonly employed to achieve high-frequency performance. Miniaturization and Integration: The demand for smaller and more compact electronic devices has driven the need for miniaturization and integration of components. High-frequency PCBs have played a significant role in enabling this trend. With advancements in manufacturing processes, it is now possible to print finer lines and spaces, allowing for denser component placement and reduced signal propagation lengths. This, in turn, leads to improved signal integrity, reduced EMI, and increased overall performance of high-frequency circuits. RF and Microwave Applications: High-frequency PCBs find extensive use in RF and microwave applications, where the ability to transmit and receive signals accurately at high frequencies is critical. These PCBs are used in radar systems, satellite communication, wireless networks, and cellular base stations, among other applications. The advancements in high-frequency PCB technology have enabled the development of advanced RF and microwave systems with enhance...
Categories
New Products
Rigid Polyimide 4-Layer PCB 1.8mm Thick HASL Lead-Free Vias Resin-filled and Capped
Taconic RF-35 PCB 2-layer 10mil 0.254mm Immersion silver High Frequency Board
F4BTME320 PCB 2-layer 1.524mm 60mil Thick Wangling F4BTME Series Immersion Tin
6-layer Hybrid PCB 0.305mm RO4003C + 3.0mm FR-4 Depth-Controlled Slot Multilayer Board
Taconic TRF-45 PCB Double-Sided 32mil 0.813mm Thick ENIG High Frequency Board
TP980 Dielectric PCB 2-Layer 4.0mm Thick DK9.8 High DK ENIG-finish High Frequency Board
TP450 PCB 2-Layer TP-series Laminates 2.5mm Thick Bare Copper
Taconic TLY-5 PCB 2-layer 125mil 3.2mm DK2.2 Laminate 1oz Copper ENIG
© Copyright: 2025 Shenzhen Bicheng Electronics Technology Co., Ltd.. All Rights Reserved.
IPv6 network supported