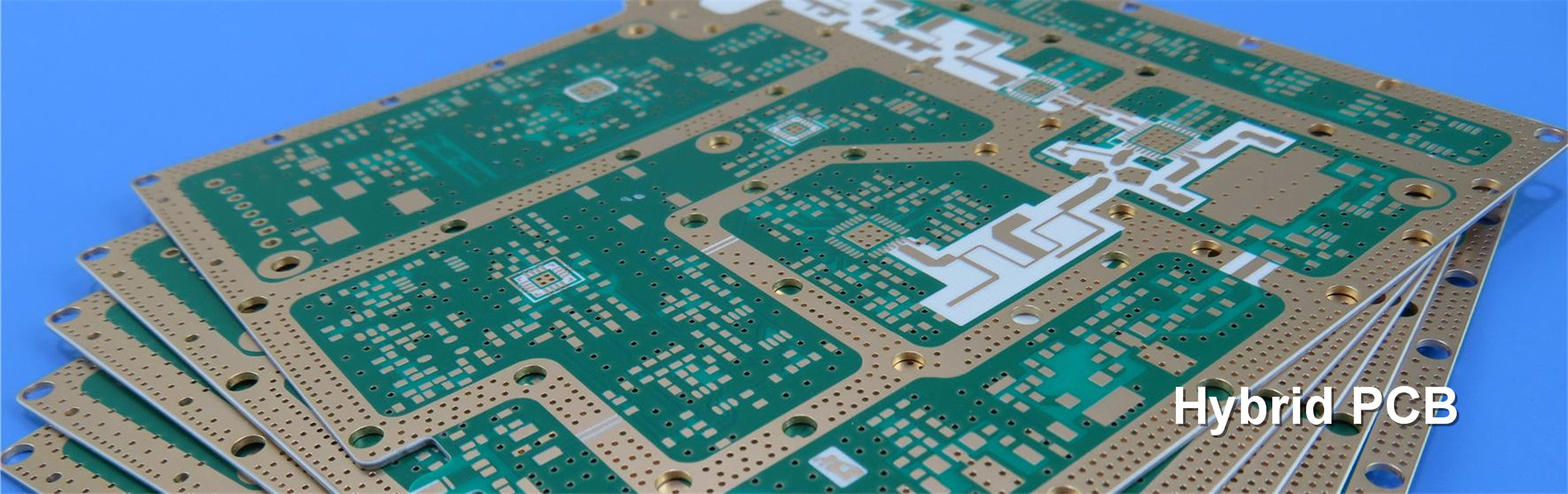
Call Us Now !
Tel : +86 755 27374946
Order Online Now !
Email : info@bichengpcb.com
Microwave composite dielectric copper-clad laminate-TP
Item NO.:
BIC-231-v296.0Order(MOQ):
1-10Payment:
T/TProduct Origin:
ChinaShipping Port:
ShenzhenLead Time:
7-10 days
TP High Frequency1.5mm Material PCB Microwave Composite Dielectric Copper-clad Laminate
Introduction
TP material is a unique high-frequency thermoplastic material in the industry. The dielectric layer of TP-type laminates consists of ceramics and polyphenylene Oxide resin (PPO), without fiberglass reinforcement. The dielectric constant can be precisely adjusted by adjusting the ratio between ceramics and PPO resin. The production process is special, and it has excellent dielectric performance and high reliability. TP refers to the smooth surface material without copper cladding, TP-1 refers to the material with copper cladding on one side, and TP-2 refers to the material with copper cladding on both sides.
Features
1. The dielectric constant can be arbitrarily selected within the range of 3 to 25 according to circuit requirements, and it is stable. Common dielectric constants include 3.0, 4.4, 6.0, 6.15, 9.2, 9.6, 10.2, 11, 16, and 20. The dielectric loss islow, and the loss increases as the frequency increases, but the change is not significant within 10 GHz.
2. Long-term operating temperature ranges from -100°C to +150°C. It has excellent low-temperature resistance. When the temperature exceeds 180°C, the material may deform, the copper foil may peel off, and there may be significant changes in electrical performance.
3. The thinnest thickness is 0.5mm, and it is available in various thicknesses and can be customized.
4. It is resistant to radiation and has low outgassing.
5. Ideal material for Beidou, missile-borne, fuze, and miniaturized antennas.
6. The adhesion between copper foil and dielectric is more reliable than ceramic substrates with vacuum coating. The material is easy to machine and can be processed through drilling, turning, grinding, shearing, etching, and other methods, which ceramic substrates cannot achieve.
7. Convenient for PCB processing, it can be processed using methods suitable for thermoplastic materials, resulting in high yield and reduced processing cost compared to ceramic substrates. Due to the characteristics of the material, it is generally not recommended for multilayer PCB processing. If multilayer PCB processing is required, low-temperature bonding sheets should be selected, and feasibility should be fully considered.
Data Sheet
Product Technical Parameter | Product Models & Data Sheet | |||||||||||||||
Product Features | Test Conditions | Unit | TP TP-1 TP-2 | |||||||||||||
Dielectric Constant |
When the dielectric constant is ≤11, the test condition is 10GHz. When the dielectric constant is >11, the test condition is 5GHz. |
/ | 3.0±0.06 | 4.4±0.09 | 6.0±0.12 | |||||||||||
6.15±0.12 | 9.2±0.18 | 9.6±0.19 | ||||||||||||||
10.2±0.2 | 11.0±0.022 | 16.0±0.4 | ||||||||||||||
20.0±0.8 | 22.0±0.88 | 25.0±1.0 | ||||||||||||||
The dielectric constant can be customized within the range of 3.0 to 25. | ||||||||||||||||
Dielectric Constant Tolerance | Dielectric Constant 3.0~11.0 | / | ±2% | |||||||||||||
Dielectric Constant 11.1~16.0 | / | ±2.5% | ||||||||||||||
Dielectric Constant 16.1~25.0 | / | ±4% | ||||||||||||||
Loss Tangent | Loss Tangent 3.0~9.5 | 10GHz | / | 0.0010 | ||||||||||||
Loss Tangent 9.6~11.0 | 10GHz | / | 0.0012 | |||||||||||||
Loss Tangent 11.1~16.0 | 5GHz | / | 0.0015 | |||||||||||||
Loss Tangent 16.1~25.0 | 5GHz | / | 0.0020~0.0025 | |||||||||||||
Dielectric Constant Temperature Coefficient | Dielectric Constant 3.0~9.5 | -55 º~150ºC | PPM/℃ | -50 | ||||||||||||
Dielectric Constant 9.6~16.0 | -55 º~150ºC | PPM/℃ | -40 | |||||||||||||
Dielectric Constant 16.1~25.0 | -55 º~150ºC | PPM/℃ | -55 | |||||||||||||
Peel Strength | 1 OZ Normal State | N/mm | >0.6 | |||||||||||||
1 OZ After AC Humidity Test | N/mm | >0.4 | ||||||||||||||
Volume Resistivity | Normal State at 500V | MΩ.cm | >1×109 | |||||||||||||
Surface Resistivity | Normal State at 500V | MΩ | >1×107 | |||||||||||||
Coefficient of Thermal Expansion (XY Z) |
Dielectric Constant 3.00~4.40 | -55 º~150ºC | PPM/℃ | 60,60,70 | ||||||||||||
Dielectric Constant 4.60~6.15 | -55 º~150ºC | PPM/℃ | 50,50,60 | |||||||||||||
Dielectric Constant 6.16~11.0 | -55 º~150ºC | PPM/℃ | 40,40,55 | |||||||||||||
Dielectric Constant 11.1~16.0 | -55 º~150ºC | PPM/℃ | 40,40,50 | |||||||||||||
Dielectric Constant 16.1~25.0 | -55 º~150ºC | PPM/℃ | 35,35,40 | |||||||||||||
Water Absorption | 20±2℃, 24 hours | % | ≤0.01 | |||||||||||||
Long-Term Operating Temperature | High-Low Temperature Chamber | ℃ | -100º~150ºC | |||||||||||||
Material Composition | Polyphenylene ether, ceramic, paired with ED copper foil. | |||||||||||||||
The density and thermal conductivity data for materials with different dielectric constants are as follows: | ||||||||||||||||
Product Features | Unit | Dielectric Constanct | ||||||||||||||
3.0 | 4.4 | 6.0 | 6.15 | 9.6 | 10.2 | 11.0 | 16.0 | 20.0 | 22.0 | 25.0 | ||||||
Density | g/cm3 | 1.69 | 1.89 | 2.1 | 2.12 | 2.26 | 2.33 | 2.40 | 2.76 | 2.73 | 2.77 | 2.94 | ||||
Thermal Conductivity | W/(M.K) | 0.40 | 0.44 | 0.55 | 0.55 | 0.65 | 0.67 | 0.70 | 0.80 | 0.85 | 0.90 | 1.0 |
Our PCB Capability (TP Series)
PCB Capability (TP Series) | |||
PCB Material: | Polyphenylene ether, ceramic | ||
Designation (TP Series) | Designation | DK | DF |
TP300 | 3.0±0.06 | 0.0010 | |
TP440 | 4.4±0.09 | 0.0010 | |
TP600 | 6.0±0.12 | 0.0010 | |
TP615 | 6.15±0.12 | 0.0010 | |
TP920 | 9.2±0.18 | 0.0010 | |
TP960 | 9.6±0.2 | 0.0011 | |
TP1020 | 10.2±0.2 | 0.0011 | |
TP1100 | 11.0±0.22 | 0.0011 | |
TP1600 | 16.0±0.32 | 0.0015 | |
TP2000 | 20.0±0.4 | 0.0020 | |
TP2200 | 22.0±0.44 | 0.0022 | |
TP2500 | 25.0±0.5 | 0.0025 | |
Layer count: | Single Sided, Double Sided PCB | ||
Copper weight: | 1oz (35µm), 2oz (70µm) | ||
Dielectric thickness (Dielectric thickness or overall thickness) | 0.5mm, 0.8mm, 1.0mm, 1.2mm, 1.5mm, 2.0mm, 3.0mm, 4.0mm, 5.0mm, 6.0mm, 7.0mm, 8.0mm, 10.0mm, 12.0mm | ||
PCB size: | ≤150mm X 220mm | ||
Solder mask: | Green, Black, Blue, Yellow, Red etc. | ||
Surface finish: | Bare copper, HASL, ENIG, Immersion silver, Immersion tin, OSP, Pure gold, ENEPIG etc.. |
A TP PCB and Applications
On the screen, you can see a 1.5mm TP high-frequency PCB with OSP (Organic Solderability Preservative) coating. TP high-frequency PCBs are also utilized in applications such as Beidou, missile-borne systems, fuzes, and miniaturized antennas.
Final Attention
The material is not suitable for 260°C thermal shock testing and cannot be wave soldered. Hand soldering with a constant temperature soldering iron is recommended. Reflow soldering is generally not recommended. If reflow soldering is carried out, the highest set temperature should not exceed 200°C, and feasibility and stability should be fully considered.
Previous:
F4BME Series Laminates High Frequency Aluminum-based PCB F4BME225Next:
F4BTM High Frequency PCB DK 3.0 F4BTM 1.524mm Substrate HASL Surface FinishesIf you have questions or suggestions,please leave us a message,we will reply you as soon as we can!
Categories
New Products
Wangling TP1020 PCB 2-Layer 4.0mm Thick ENIG TP Series High Frequency Substrates
TFA615 PCB 2-layer 0.508mm 20mil Thick DK6.15 ENIG TFA Series Substrates
Rogers RT/duroid 6202 PCB 2-layer 5mil 0.127mm ENIG Custom High Frequency Board
RT/duroid 6035HTC PCB 2-layer 30mil 0.762mm ENIG No Solder Mask Black Silkscreen
RT/duroid 5880 PCB 2-layer Rogers 5880 15mil Thick Immersion Gold Green Solder Mask
Rogers RO4725JXR PCB 2-layer 30.7mil ENIG 35μm Copper Bare Board
RO4350B PCB 2-layer Rogers 4350B 16.6mil ENEPIG 35μm Copper Green Solder Mask
RO4003C PCB 2-layer Rogers 4003C Substrate 16mil ENIG 1oz Copper Black Silkscreen
© Copyright: 2025 Shenzhen Bicheng Electronics Technology Co., Ltd.. All Rights Reserved.
IPv6 network supported